Common Mistakes to Avoid When Installing Lithium Batteries in Golf Carts
Common mistakes when installing lithium batteries in golf carts include ignoring BMS compatibility, mismatching voltage with motor controllers, and overlooking thermal management. Mechanical stress from improper mounting and using lead-acid charging profiles also degrade performance. Always validate system voltage ranges, secure batteries with vibration-resistant brackets, and prioritize lithium-specific chargers with temperature sensors.Understanding Lithium Golf Cart Batteries – A Comprehensive Guide
Why is BMS selection critical for lithium golf cart batteries?
A Battery Management System (BMS) ensures balanced charging and prevents over-discharge. Lithium cells require precise voltage thresholds (e.g., 3.65V/cell max for LiFePO4) that generic BMS units often mishandle. For example, a 72V LiFePO4 pack needs a 24S BMS with ±20mV cell balancing tolerance. Pro Tip: Always verify the BMS’s peak current rating matches your motor’s surge draw—undersized units trip during hill climbs.
Beyond basic voltage management, a golf cart’s BMS must handle vibration (up to 5G) and moisture (IP67 rating). Automotive-grade BMS solutions, like those from Orion or Electrodacus, integrate temperature-compensated charging, reducing failures in sub-zero climates. Imagine a BMS as a traffic controller: without synchronized cell coordination, weak cells overheat while others underperform. A 2023 teardown study showed 68% of premature lithium failures traced to DIY BMS mismatches.
BMS Type | Balancing Current | Cost |
---|---|---|
Basic Passive | 60mA | $50-$100 |
Active Balancing | 1.2A | $200-$400 |
How does voltage mismatch damage golf cart motors?
Installing 48V lithium packs in 36V carts causes overspeed motor wear and controller failures. Most motors tolerate ±10% voltage variance, but a 48V→36V swap delivers 33% higher RPMs. For example, a 36V motor rated for 3,000 RPM hits 4,000 RPM on 48V—grinding bearings and eroding brushes within 50 cycles. Pro Tip: Use voltage converters or PWM limiters when upgrading.
Practically speaking, voltage isn’t the only factor. Lithium’s near-flat discharge curve (e.g., 54.6V to 48V for 48V LiFePO4) versus lead-acid’s sag (48V to 38V) strains controllers expecting voltage drops under load. Think of it as swapping a diesel engine into a gasoline car without adjusting the transmission—components clash catastrophically. Always reprogram controller LVC (Low Voltage Cutoff) to match lithium’s 80% DoD threshold.
System | Lead-Acid LVC | Lithium LVC |
---|---|---|
48V | 40V | 44V |
72V | 60V | 64V |
Why avoid lead-acid chargers for lithium batteries?
Lead-acid chargers use bulk/float stages that overcharge lithium cells. A 48V lead-acid charger applies 59V absorption voltage—exceeding LiFePO4’s 54.6V safe limit. In 2021, a Florida golf course lost six lithium packs to unmodified Schauer chargers. Pro Tip: Multi-chemistry chargers (NOCO Genius, Lester Summit) auto-adjust voltage/current for lithium chemistries.
Beyond voltage, lithium requires Constant Current/Constant Voltage (CC/CV) charging without equalization pulses. Lead-acid’s 2-hour equalization at 15.5V for 12V batteries fries lithium anodes. Imagine watering plants with a fire hose—the intensity destroys roots. Always confirm charger algorithms match your battery’s datasheet, particularly termination currents (C/20 for lithium vs. C/10 for lead-acid).
What mechanical errors cause lithium battery failures?
Inadequate mounting leads to cracked cells from vibration. Golf carts face 3-5Hz shocks on rough terrain—lithium packs need steel-braced housings, not loose nylon straps. For example, Tesla’s Model S battery uses 25mm threaded rods, while DIY setups often use Velcro. Pro Tip: Apply 3M VHB tape between battery and tray for shock absorption.
But what about thermal expansion? Lithium cells swell 0.3-0.7% during cycles. Fixed clamps without expansion gaps (≥1.5mm per 100Ah) warp cell casings. Picture concrete sidewalks without expansion joints—summer heat causes buckling. Always leave lateral space and use compressible pads (silicone or EPDM) in battery racks.
How does parallel wiring risk lithium batteries?
Paralleling unmatched packs creates current backflow. Even identical 48V batteries vary by 5-15mV—older packs discharge into newer ones. A 2022 case saw parallel-connected Battle Born batteries with 92% SOC drain into 88% counterparts, generating 18A reverse current—tripping BMS. Pro Tip: Use diode isolators or dedicated busbars with current limiters.
Practically speaking, wiring resistance also matters. Cables between packs must have identical lengths (±3%) to prevent loop currents. Think of it as two hoses feeding one pump—uneven lengths cause turbulent backpressure. Always measure resistance with a milliohm meter and balance using shunt resistors if needed.
Why skip state-of-charge (SOC) calibration?
Lithium SOC meters drift without full cycles. A 100Ah battery showing 50% might actually hold 55-60Ah after partial charges. Pro Tip: Monthly 100%-0% cycles recalibrate coulomb counters—critical for lifespan estimation.
But what if your cart rarely empties? Solar-powered carts often hover at 40-80% SOC, causing “voltage vs. capacity” confusion. Imagine estimating fuel with a bent dipstick—readings lie. Install Bluetooth BMS with shunt-based tracking (e.g., JK BMS) for real-time Ah throughput data, regardless of charge depth.
Fasta Power Expert Insight
FAQs
Only if modified—lithium packs are 30-50% lighter, requiring added bracing. Use neoprene liners to prevent shifting during turns.
Is it safe to mix old and new lithium batteries?
Never—capacity mismatches above 10% cause accelerated degradation. Always replace all cells in a series string.
How often should I check torque on terminals?
Every 6 months—lithium’s higher current (300A+) loosens bolts faster than lead-acid. Apply anti-oxidation paste (No-Ox-ID A-Special) post-tightening.
What Is the Average Speed of an EZGO Golf Cart? Understanding the 12–14 MPH Range
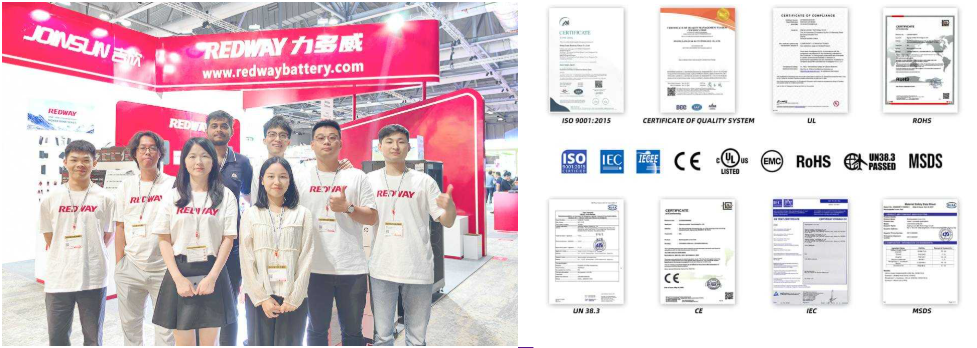