DIY Installation: Upgrading Your Golf Cart to Lithium Power
Upgrading your golf cart to lithium power involves replacing lead-acid batteries with lithium-ion cells, offering longer lifespan (2,000–5,000 cycles), 50–70% weight reduction, and faster charging. Key steps include assessing voltage compatibility (e.g., 36V/48V to 72V), installing a BMS, and rewiring. Safety is critical—always disconnect the cart’s power and use insulated tools. Lithium packs like LiFePO4 deliver stable 12.8V per cell, matching most carts’ nominal voltage. Understanding Lithium Golf Cart Batteries – A Comprehensive Guide
Is my golf cart compatible with lithium batteries?
Compatibility depends on voltage, controller, and physical space. Most 36V/48V carts transition seamlessly to lithium if the BMS aligns with motor draw. Measure your battery tray and confirm max discharge rates (e.g., 100A BMS for 500W motors). Pro Tip: Older resistor-based controllers may need upgrades to handle lithium’s low internal resistance.
Golf carts built after 2000 typically use solid-state controllers compatible with lithium. For example, a 48V Club Car with 8×6V lead-acid batteries can swap to a 48V 100Ah LiFePO4 pack, gaining 80% more runtime. However, carts with analog throttles or outdated PWM systems may require $150–$300 controller upgrades. Beyond voltage, ensure the lithium pack’s dimensions fit your tray—most drop-in replacements are 10–30% smaller. A rhetorical question: Why risk stranded energy when precise sizing ensures seamless power delivery?
What tools are needed for lithium conversion?
Essential tools include insulated wrenches, a multimeter, terminal brush, and torque wrench. You’ll also need heat-shrink tubing, busbars, and a BMS with temperature sensors. Pro Tip: Label all cables during removal to avoid reversed polarity.
Start by disconnecting the old batteries—prioritize the negative terminal first. Use an 8–10mm wrench for lead terminals, then clean corrosion with baking soda and a terminal brush. When installing lithium, torque terminals to manufacturer specs (usually 4–6 N·m) to prevent arcing. A multimeter ensures each cell stays balanced (3.2–3.65V for LiFePO4). Practically speaking, converting a 48V cart takes 2–4 hours for novices. Still, a pro might finish in 90 minutes. Remember, lithium’s lighter weight reduces strain, but improper busbar alignment risks short circuits.
Item | Lead-Acid | Lithium |
---|---|---|
Weight (48V) | 290–350 lbs | 70–100 lbs |
Cycle Life | 500–800 | 2,000–5,000 |
Recharge Time | 8–10 hrs | 2–4 hrs |
How to ensure safe lithium installation?
Safety protocols require disconnecting all power, wearing gloves/glasses, and using a BMS. Isolate battery terminals with electrical tape and avoid metal contact. Pro Tip: Test the BMS’s low-voltage cutoff before final assembly.
Lithium cells are sensitive to over-discharge—set your BMS to disconnect at 2.5V per cell (30V for 48V packs). Use a thermal camera or infrared thermometer to monitor connections during initial testing. For example, a loose terminal might spike from 25°C to 60°C under load, signaling resistance issues. Beyond physical safety, configure the charger to match lithium profiles—lead-acid chargers can overcharge cells, triggering thermal runaway. Transitional note: While lithium is robust, neglecting these steps risks $500–$2,000 in replacements. What’s worse than a weekend project becoming a fire hazard?
Step-by-step lithium installation guide
Follow these steps: 1) Remove lead-acid batteries. 2) Clean terminals/tray. 3) Install lithium pack/BMS. 4) Test voltage/connections. 5) Secure with brackets. 6) Calibrate charger. Pro Tip: Use anti-vibration pads to protect cells.
After removing old batteries, scrub the tray with vinegar to neutralize acid residue. Position the lithium pack centrally, ensuring cables reach terminals without strain. Connect the BMS between the battery and controller, routing sense wires in order (cell 1 to cell 16). Secure packs with steel straps or brackets—lithium’s light weight doesn’t eliminate movement risks. Finally, perform a low-speed test drive to verify power delivery. For instance, a 48V EcoBattery kit typically adds 5–8 mph and 30% hill-climbing torque. A rhetorical question: Why settle for sluggish performance when precise installation unlocks full potential?
Cost Factor | Lead-Acid | Lithium |
---|---|---|
Initial | $600–$900 | $1,500–$2,800 |
5-Year Total | $1,800+ | $1,500–$2,000 |
Warranty | 1 year | 3–10 years |
Why is a BMS critical for lithium conversions?
The Battery Management System (BMS) monitors cell balance, temperature, and voltage. It prevents overcharge/over-discharge and balances cells during charging. Pro Tip: Choose a BMS with Bluetooth for real-time monitoring.
A quality BMS (e.g., 100A Daly or ANT) ensures even wear across cells, extending pack life by 20–40%. For example, a 16S LiFePO4 BMS manages 16 cells, maintaining ±0.05V balance. Without it, cell drift could reduce capacity by 30% within 50 cycles. Transitionally, while BMS adds $100–$300 to the project, it’s cheaper than replacing a $1,500 pack. Warning: DIYers skipping the BMS risk “runaway” imbalances—like a misaligned wheel eventually causing a blowout.
Fasta Power Expert Insight
FAQs
Most 36V/48V carts are compatible, but check controller type and tray size. Older resistor-coil carts may need controller upgrades for lithium’s low resistance.
Do I need a new charger for lithium?
Yes—lithium requires CC-CV chargers with voltage limits. Using lead-acid chargers risks overcharging; choose a 58.4V charger for 48V LiFePO4 systems (±0.5V tolerance).
How to Determine the Year of Your EZGO Golf Cart Using the Serial Number
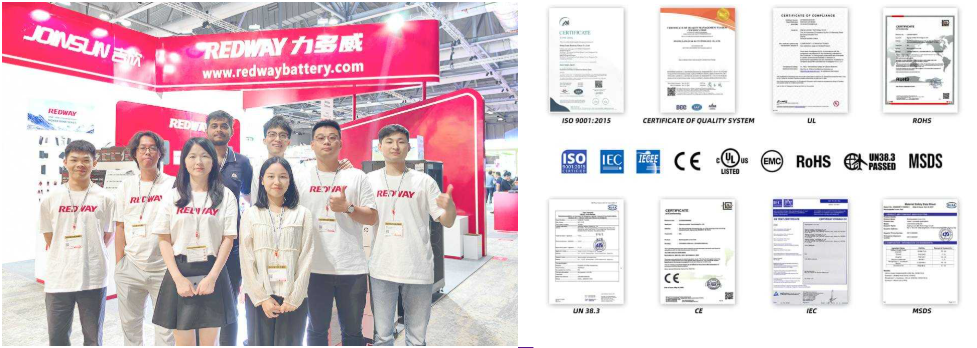