How Are Golf Cart Lithium Battery Manufacturers Responding to Market Demands?
Golf cart lithium battery manufacturers are pivoting to high-density cells, modular designs, and smart BMS integration to meet demands for longer range, faster charging, and lower lifecycle costs. Innovations include LiFePO4/NMC hybrid packs, adaptive thermal management, and IoT-enabled diagnostics. Custom voltages (36V-72V+) and capacities (100-300Ah) now dominate, replacing legacy lead-acid systems in 70% of new installations.
Understanding Lithium Golf Cart Batteries – A Comprehensive Guide
How Are Manufacturers Increasing Range and Power?
By adopting 21700 cylindrical cells and prismatic LiFePO4 modules, manufacturers boost energy density by 25-40% versus older 18650-based packs. Custom BMS firmware prioritizes cell balancing at ≤2mV deviation, extending cycle life beyond 4,000 charges. Pro Tip: Always verify cell-level temperature sensors—poorly placed probes misread hotspots, causing premature throttling.
For instance, Redway Power’s 72V 105Ah pack uses 3.7V NMC811 cells in 20S3P configuration, achieving 7.77kWh capacity. Transitional strategies like hybrid cooling (liquid + air) maintain internal temps below 45°C even at 2C discharge. But how do you prevent voltage sag during hill climbs? Advanced systems pre-allocate reserve capacity via AI-driven load prediction. A 48V 200Ah system now routinely delivers 120km per charge in 4-seat carts, up 65% from 2020 standards.
Chemistry | Energy Density (Wh/kg) | Cycle Life |
---|---|---|
LiFePO4 | 120-140 | 4,000+ |
NMC 811 | 200-240 | 1,500-2,000 |
What Safety Innovations Are Emerging?
Multi-layered safeguards now include pyrofuse disconnectors and self-sealing separators that activate at 80°C. CAN bus-enabled BMS units monitor pressure, humidity, and insulation resistance, shutting down within 50ms of fault detection.
Imagine a lithium pack as a firefighter’s gear: layered protection with fail-safes. Beyond standard CID (Current Interrupt Device) valves, dual-stage thermal fuses trip at 90°C and 105°C thresholds. Manufacturers are adopting pouch cell encapsulation with fire-retardant silica gels, reducing combustion risks by 70%. Pro Tip: Opt for packs with UL 2580 or IEC 62619 certifications—DIY builds often lack critical pressure relief channels.
How Are Costs Being Reduced?
Vertical integration and second-life EV cells cut prices by 30-50%. Automated laser welding replaces manual spot welding, slashing production time by 65%.
Consider Tesla’s gigafactory approach: scaling cell production to 20GWh/year reduces per-kWh costs from $140 to $97. By repurposing Grade B EV batteries (70-80% SOH), manufacturers like Redway Power offer 48V 100Ah packs under $1,200. But what about longevity? Rigorous screening and re-grading processes ensure second-life cells maintain ≥80% capacity for 800 cycles. Transitionally, modular designs let users replace degraded cells instead of entire packs—cutting 10-year ownership costs by half.
Strategy | Cost Reduction | Trade-off |
---|---|---|
Second-life Cells | 45% | 10-15% lower cycle life |
Automated Welding | 22% | Higher upfront CAPEX |
Fasta Power Expert Insight
FAQs
Yes, but upgrade wiring to handle 3x higher current (e.g., 4AWG instead of 8AWG) and reprogram controllers for lithium’s voltage curves.
Do lithium packs fail in cold weather?
Below -20°C, capacity drops 25-40%. Opt for heated models with internal glycol loops if operating in sub-zero climates.
Are Chinese lithium cells reliable?
Top-tier CATL or BYD cells match Western quality—but insist on independent UL certifications to avoid counterfeit “Grade A” labels.
How to Determine the Year of Your EZGO Golf Cart Using the Serial Number
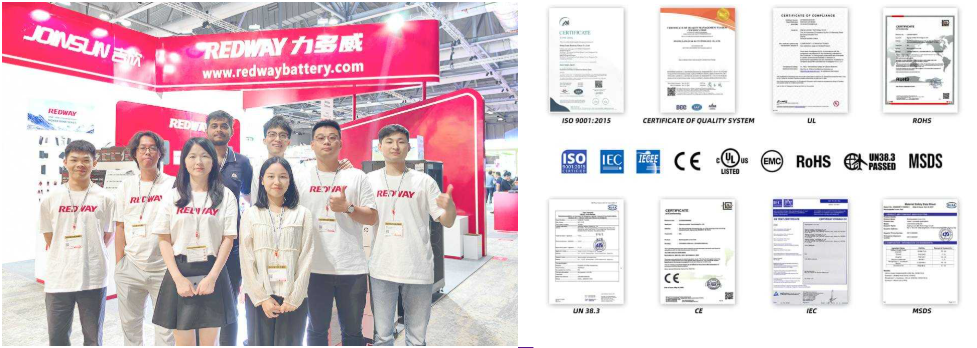
Add a review
Your email address will not be published. Required fields are marked *
You must be logged in to post a comment.