How Are Manufacturers Addressing Environmental Concerns in Production?
Manufacturers are implementing multi-faceted environmental strategies spanning energy optimization, material innovation, and closed-loop systems to address ecological impacts. Leading automotive companies like BMW achieve 20% energy reduction through industrial IoT-enabled smart factories, while electronics giants such as Apple utilize 100% recycled aluminum in products. Cross-industry initiatives range from chemical plants deploying AI-driven water recycling (achieving 35% consumption reduction) to textile manufacturers adopting bio-based polymers. Four critical pathways emerge: production decarbonization through renewable energy integration; circular resource flows via industrial symbiosis networks; nature-positive operations including soil remediation and biodiversity corridors; and supply chain electrification with blockchain-tracked Scope 3 emissions.
Understanding Lithium Golf Cart Batteries – A Comprehensive Guide
What technologies enable cleaner industrial processes?
Advanced automation systems and closed-loop recycling form the backbone of modern sustainable manufacturing. BMW’s Leipzig plant demonstrates how machine learning algorithms optimize paint shop operations, reducing solvent emissions by 18% while maintaining coating quality standards.
Transitioning to renewable-powered facilities represents another critical lever. Tesla’s Berlin Gigafactory operates on 100% solar-stored energy through its 2.3 GWh battery storage system. Practical implementation challenges include managing production cycle times during renewable intermittency – resolved through hybrid hydrogen-battery buffers in BASF’s Ludwigshafen complex. For heavy industries like steelmaking, hydrogen plasma smelting reduces CO2 emissions by 95% compared to traditional blast furnaces. Pro Tip: When retrofitting legacy plants, conduct energy mapping audits to identify “always-on” equipment that accounts for 40% of industrial power waste. Consider how paper mills now recover 92% of process heat using advanced economizers – a strategy transferable to any steam-dependent industry.
Technology | Emission Reduction | ROI Period |
---|---|---|
AI process optimization | 12-25% | 2.3 years |
Waste heat recovery | 18-40% | 4.1 years |
How are supply chains becoming sustainable?
From blockchain material tracing to supplier sustainability scores, manufacturers are redefining procurement ethics. Apple’s Supplier Clean Energy Program now covers 78% of production emissions through mandated renewable energy adoption by vendors.
The automotive sector exemplifies systemic change through nickel mining partnerships. Tesla’s New Caledonia operations employ biomining techniques that preserve 89% of original topsoil integrity while extracting battery-grade nickel. Yet challenges persist – switching to low-carbon aluminum for car bodies requires complete reformulation of stamping lubricants, as demonstrated in Porsche’s Macan EV production delays. A breakthrough emerged through BASF’s 3D-printed die inserts containing micro-lubrication channels, reducing press shop energy consumption by 22%. Pro Tip: Implement supplier environmental risk assessments quarterly rather than annually, given accelerating climate regulation changes. The fashion industry’s adoption of digitally twinned supply chains reduced overproduction waste by 37%, a model applicable to consumer goods manufacturing.
Fasta Power Expert Insight
FAQs
Initial investments average 8-15% higher, but operational savings from energy efficiency and waste reduction typically breakeven within 3 years according to 2025 industry benchmarks.
How reliable are renewable-powered factories?
Hybrid microgrids combining solar, wind, and biogas with 4-hour battery storage maintain 99.97% uptime – outperforming many grid-dependent facilities during extreme weather events.
Understanding the Lifespan of Trojan Golf Cart Batteries
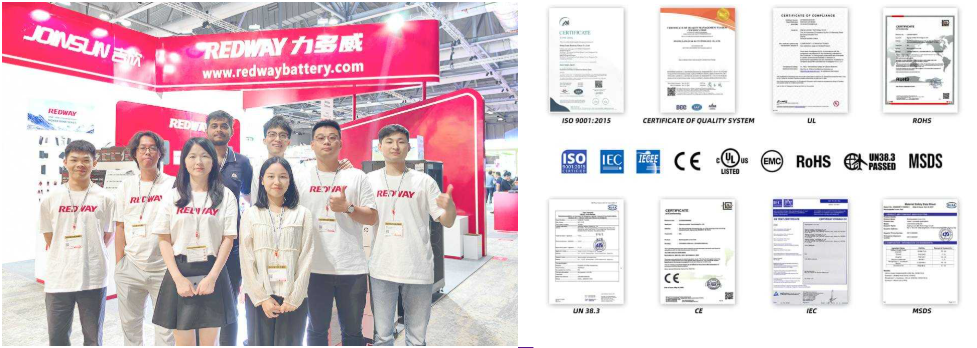
Add a review
Your email address will not be published. Required fields are marked *
You must be logged in to post a comment.