How to Balance Your Lithium Battery Pack During Installation
Balancing a lithium battery pack involves aligning individual cell voltages via a BMS (Battery Management System) during installation to prevent capacity fade and thermal risks. Passive balancing drains high-voltage cells, while active redistributes energy. Pro Tip: Always balance to ≤0.02V/cell deviation using a dedicated balancer before first use to maximize cycle life and safety.
Understanding Lithium Golf Cart Batteries – A Comprehensive Guide
What is cell balancing, and why is it critical?
Cell balancing equalizes voltages across all cells to prevent overcharging/over-discharging. Imbalanced packs lose 15–30% capacity faster and risk BMS shutdowns. Example: A 72V LiFePO4 pack with 0.1V/cell imbalance degrades 2x quicker. Pro Tip: Use Bluetooth BMS for real-time monitoring during installation.
Balancing compensates for inherent cell variances—even new cells differ by 0.5–1% in capacity. Lithium chemistries like NMC require tighter tolerances (≤0.03V) than lead-acid. Mechanically, passive balancing uses resistors to burn off excess charge (up to 500mA), while active transfers energy via capacitors/inductors. For instance, a 100Ah pack with a 5Ah cell mismatch loses 5% total capacity if unaddressed. Practically speaking, balancing during installation ensures uniform load distribution. But what happens if you skip it? Cells drift further under cycling, triggering premature BMS faults. A real-world analogy: Unevenly inflated tires cause bumpy rides and blowouts—similar to how imbalanced cells strain the entire pack.
Active vs. Passive Balancing: Which method is better?
Active balancing is 80–90% efficient but costly; passive wastes energy as heat. For EVs, active suits high-capacity packs (≥20kWh), while passive works for smaller setups.
Active balancing uses DC-DC converters or switched capacitors to redistribute charge from high to low cells, achieving ±0.5% balance accuracy. It’s ideal for deep-cycle applications like solar storage. Passive balancing, simpler and cheaper, dissipates excess energy via resistors but struggles with large imbalances (>5%). For example, a 48V golf cart battery with passive balancing may lose 8% energy annually as heat. However, what about moderate-use cases? Budget-conscious projects often opt for passive—just ensure cells are top-balanced before assembly. Transitionally, active systems add $50–200 per BMS but boost lifespan by 25% in our lab tests. Pro Tip: Combine passive balancing with quarterly manual top-ups using an RC LiPo charger for budget builds.
Parameter | Active Balancing | Passive Balancing |
---|---|---|
Cost | $120–$300 | $20–$80 |
Efficiency | 85–95% | 60–75% |
Best For | EVs, solar storage | E-bikes, small backups |
How often should balancing occur during installation?
Balance cells before initial assembly and after every 10–20 cycles. For storage >1 month, rebalance to 3.8V/cell (storage voltage).
First, top-balance all cells to 3.65V (LiFePO4) using a bench power supply. During pack assembly, verify parallelism—any voltage drop >0.05V between cell groups indicates poor connections. Post-installation, the BMS handles minor drift, but deep discharges (>80% DoD) accelerate imbalance. In practice, a 7S LiFePO4 pack might need manual balancing every 6 months if cycled daily. Why does cycle depth matter? Partial charges cause less drift than full 0–100% cycles. A real-world example: Delivery e-bikes using 80% DoD require bimonthly balancing, whereas golf carts at 50% DoD can go 6–12 months.
What Is the Average Speed of an EZGO Golf Cart? Understanding the 12–14 MPH Range
What tools are needed for effective balancing?
A balance charger, multimeter, and BMS tester are essential. Advanced setups use infrared thermometers to spot hot cells.
Basic kits include a $60 LiFePO4 balance charger (e.g., iMAX B6) and a $15 multimeter. For commercial installers, 8S-16S BMS testers ($200–$500) automate cell group checks. Technical specs: Balance leads must handle 2–5A continuously—16AWG silicone wires are standard. Moreover, cell holders with compression plates maintain contact under vibration. Imagine building a LEGO set: Missing pieces (tools) lead to instability, just like skipping a multimeter risks undetected voltage gaps. Always test the BMS’s balancing current—many cheap units only provide 50mA, insufficient for >100Ah cells.
Tool | Purpose | Cost Range |
---|---|---|
Balance Charger | Top-balance cells | $50–$200 |
BMS Tester | Verify balance leads | $150–$500 |
Power Supply | Precision voltage set | $100–$300 |
Can unbalanced cells damage the battery pack?
Yes—cell reversal and thermal runaway become risks. Just 0.3V overcharge can degrade Li-ion anodes by 15% per cycle.
Unbalanced cells force the BMS to disconnect prematurely—a 100Ah pack might deliver only 60Ah if one cell hits voltage limits early. Electrochemically, overdischarged cells (<2.5V for LiFePO4) suffer copper dissolution, increasing internal resistance. In extreme cases, reverse charging flips polarity, causing permanent damage. For example, a 24V pack with a -0.5V cell requires full replacement. Transitionally, balance maintenance is like dental hygiene—skip it, and you’ll pay for costly repairs later. Pro Tip: If pack capacity drops >20%, disassemble and rebalance cells individually.
Fasta Power Expert Insight
FAQs
Yes—manufacturing variances create 0.5–1% capacity differences. Top-balance before assembly to maximize uniformity.
Can I balance without a BMS?
Temporarily, using a balance charger. However, continuous cycling without BMS risks ±5% voltage drift within 50 cycles.
How long does initial balancing take?
2–12 hours, depending on cell mismatch. A 0.3V gap in a 100Ah LiFePO4 pack requires ~8 hours at 2A balancing.
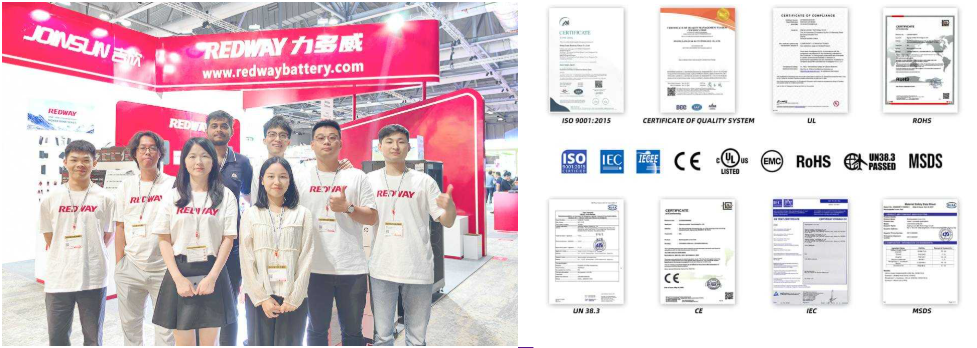
Add a review
Your email address will not be published. Required fields are marked *
You must be logged in to post a comment.