How to Connect Multiple Lithium Batteries in a Golf Cart
Connecting multiple lithium batteries in a golf cart involves series or parallel wiring to match voltage and capacity requirements. For example, two 36V LiFePO4 batteries in series create a 72V system, while parallel connections increase Ah for extended range. Proper BMS integration, balanced cells, and identical battery specs are critical to prevent thermal runaway or capacity mismatches. Always use matched capacity/age batteries and fuse interconnects.
Understanding Lithium Golf Cart Batteries – A Comprehensive Guide
What configurations are used for multi-battery setups?
Golf carts use series, parallel, or series-parallel configurations to achieve target voltage/capacity. Series wiring adds voltages (e.g., four 12V batteries = 48V), while parallel increases Ah. Hybrid setups like 2S2P (two series strings paralleled) balance power and runtime.
Series connections dominate golf carts to meet 48V/72V system needs. Let’s break it down: Two 24V LiFePO4 batteries in series create a 48V pack, while three 24V units hit 72V. But parallel configurations require meticulous attention—capacity variances over 5% trigger BMS isolation. Real-world example: Four 12V 100Ah batteries in series form a 48V 100Ah pack (4.8kWh), sufficient for 25–30 miles per charge. Pro Tip: Use a busbar for clean parallel connections, reducing resistance by 30% versus daisy-chained cables. Transitioning from theory, why prioritize cell balancing? Because unmatched internal resistances in parallel cells cause uneven load distribution, accelerating degradation. Always validate voltage synchronization with a multimeter post-installation.
Configuration | Voltage | Capacity |
---|---|---|
Series | Sum of batteries | Equal to single battery |
Parallel | Equal to single battery | Sum of batteries |
How does BMS affect multi-battery setups?
A Battery Management System (BMS) monitors cell voltages, temperatures, and current in lithium packs. Multi-battery systems require centralized or distributed BMS architectures to ensure synchronization and prevent over-discharge.
Centralized BMS units simplify monitoring but demand high amperage tolerance (100A+ for golf carts). Distributed systems use slave modules per battery, allowing granular control but adding wiring complexity. For example, four 12V batteries in series need a 48V BMS with cell-level balancing. Pro Tip: Opt for BMS with passive balancing (50–100mA) for cost-sensitive builds, or active balancing (500mA+) if packs differ by >2% capacity. But how does this play out practically? An imbalanced 72V pack with 0.3V cell variance loses 15% capacity within 50 cycles. Transitioning to real-world solutions, golf cart owners should prioritize BMS with temperature cutoffs (65°C/149°F) to prevent overheating during hill climbs.
BMS Type | Voltage Range | Balancing Current |
---|---|---|
Passive | 12–72V | 50–100mA |
Active | 24–96V | 500mA–2A |
What wiring standards ensure safety?
Use tinned copper cables, 150A fuses, and anti-spark connectors rated for 2x the system’s max current. 48V systems need 6 AWG wiring for runs under 3ft, while 72V setups demand 4 AWG to minimize voltage drop.
High-current golf carts (600A+ peak) require welding-grade cables with 105°C insulation. For instance, a 72V cart drawing 300A needs 4 AWG cables—anything thinner risks 5V+ drop under load, triggering BMS shutdowns. Pro Tip: Crimp terminals with hydraulic tools—solder joints fail under vibration. Transitioning to connectors, Anderson SB175 handles 175A continuously and features polarity keys to prevent reversal. Ever wonder why color coding matters? Red/black schemes prevent accidental shorts, especially when adding auxiliary loads like LED lights.
Can you expand existing lithium battery systems?
Yes, but only with identical voltage, capacity, and chemistry batteries. Adding mismatched units creates imbalance, forcing newer batteries to compensate and degrade prematurely.
When expanding a 48V 100Ah LiFePO4 system, introduce batteries from the same production batch with ≤5% capacity variance. Cycle the new units individually to 50% SoC before integrating—this reduces stress during initial equalization. For example, adding a 120Ah battery to a 100Ah pack cuts the former’s lifespan by 40% within a year. Transitioning to maintenance, monthly SoC checks via Bluetooth BMS apps (like Xiaoxiang) help detect outliers early. Ever faced sudden capacity drops? That’s often a single underperforming cell dragging down the entire system.
What are the risks of improper multi-battery setups?
Thermal runaway, BMS failures, and voltage spikes top the list. Cross-connected polarities or imbalanced cells can ignite lithium packs, especially in unventilated compartments.
In a case study, paralleling a 95Ah and 100Ah battery without balancing caused 20A internal circulation current—overheating the weaker pack’s cells. Always use diodes or balancing boards for parallel links. Pro Tip: Install a 500A mega fuse within 12″ of the battery bank—it interrupts faults within milliseconds. Transitioning to real-world protocols, NASA-style “triple redundancy” applies: fuse + circuit breaker + BMS protection. Why risk it? A single $15 fuse could save $2,000 in battery replacements.
Fasta Power Expert Insight
FAQs
Only if identical in make/model/age. Mixing old and new strains packs, reducing lifespan by 30–50%.
Do parallel batteries need separate BMS?
No—use a single BMS rated for total current. Dual BMS setups can conflict, causing false triggers.
How to check if batteries are balanced?
Measure individual voltages at full charge. A >0.05V difference requires rebalancing via discharger or manual adjustment.
How to Determine the Year of Your EZGO Golf Cart Using the Serial Number
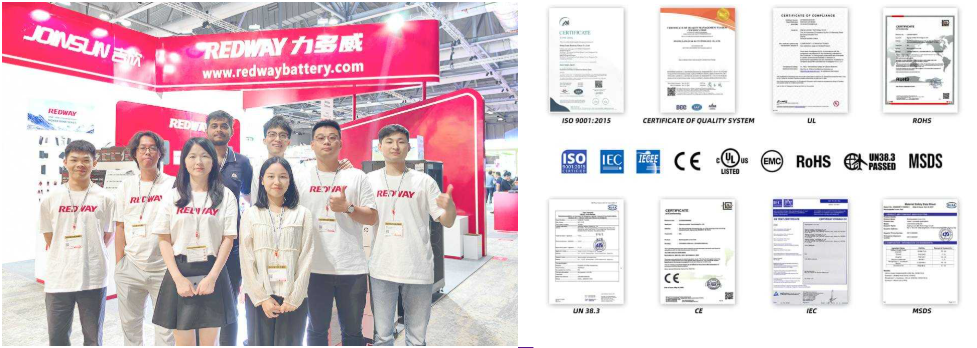