How to Mount and Secure Lithium Batteries in Your Golf Cart
Mounting lithium batteries in golf carts requires secure fastening to prevent movement, vibration damage, and electrical shorts. Key steps include using rigid steel brackets, vibration-dampening pads, and corrosion-resistant hardware (e.g., M8 bolts). Position batteries flat, away from heat sources, with a low center of gravity. Lithium’s lightweight design allows flexible placement but demands precise BMS alignment. Pro Tip: Always insulate terminals and torque bolts to 12–15 Nm.
Understanding the Lifespan of Trojan Golf Cart Batteries
Why is secure mounting critical for lithium golf cart batteries?
Secure mounting prevents terminal arcing, cell misalignment, and BMS disconnections caused by vibration. Lithium batteries lack the weight of lead-acid, making them prone to shifting during abrupt turns. A 20% loose battery can reduce lifespan by 40% due to micro-cracks in cells.
Lithium cells are sensitive to physical stress. For example, a battery shifting just 1 cm can stretch busbars, causing intermittent faults. Pro Tip: Use 3M VHB tape between brackets and frame for adhesive reinforcement. Technically, ideal mounting setups include:
– Steel brackets with 2 mm thickness
– 70A vibration dampeners (shore hardness)
– Terminal covers rated for 1000V
Transitional phrase: Beyond bolt tightness, alignment matters—misplaced batteries strain wiring. A golf cart on a bumpy course subjects batteries to 5–7G forces, mimicking a smartphone dropped weekly.
Secure Mounting | Insecure Mounting |
---|---|
15+ years lifespan | 3–5 years lifespan |
Stable voltage output | Voltage spikes/drops |
How to choose the right location for lithium batteries?
Prioritize weight distribution and accessibility. Front compartments improve handling, but rear placements simplify wiring. Avoid areas near motors (>60°C) or exposed to water splash zones.
Under-seat mounting cuts cable length by 50%, reducing resistance. However, rear trunk locations offer 30% more space for larger packs. Pro Tip: Measure twice—lithium’s compact size doesn’t justify cramming. For instance, Club Cars need 5 cm clearance around batteries for airflow. Transitional phrase: Practically speaking, map existing wiring before finalizing positions to avoid $200+ in rerouting costs.
What hardware ensures reliable battery mounting?
Use grade 8.8 bolts and steel locknuts. Polymer-coated stainless steel resists corrosion from road salts. Avoid aluminum—it fatigues after 5000 vibration cycles.
A complete kit includes:
– 4x M8x40mm bolts
– Spring washers
– 10mm rubber isolators
Pro Tip: Apply Loctite 243 to bolt threads—it withstands 100°C and prevents loosening. Transitional phrase: Contrary to assumptions, thicker isn’t always better: oversized brackets add weight without improving stability. For example, EZGO installations often use 3/16″ steel plates, which handle 300 lbs lateral force.
Component | Lead-Acid | Lithium |
---|---|---|
Bracket Thickness | 1.5 mm | 2.0 mm |
Hardware Grade | Grade 5 | Grade 8 |
Fasta Power Expert Insight
Understanding Lithium Golf Cart Batteries – A Comprehensive Guide
FAQs
Only if reinforced—lithium’s 60% lighter weight reduces friction, requiring added anti-shift brackets or adhesive-backed foam.
Are vibration dampeners necessary on paved paths?
Yes—even smooth roads generate 20–50 Hz vibrations, accelerating weld fatigue. Neoprene pads reduce peak G-forces by 70%.
How often should I check mounting bolts?
Inspect every 50 hours of operation. Bolts loosen 0.2% per 10 vibration cycles—retorque annually.
What if my battery moves slightly after installation?
Add 1/8″ silicone spacers between brackets. Persistent motion indicates undersized hardware—upgrade to M10 bolts.
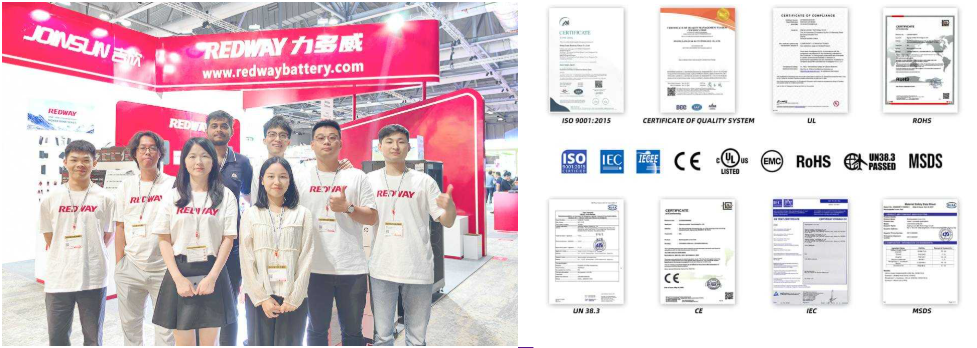
Add a review
Your email address will not be published. Required fields are marked *
You must be logged in to post a comment.