How to Test Your Golf Cart After Installing a Lithium Battery
Testing your golf cart after installing a lithium battery ensures safe operation, optimal performance, and battery longevity. Start by verifying voltage levels with a multimeter, checking BMS (Battery Management System) functionality, and conducting a load test. For example, a 48V lithium pack should maintain 53–54V under load. Pro Tip: Avoid testing in wet conditions—lithium batteries are water-resistant but susceptible to terminal corrosion if exposed repeatedly.
Understanding Lithium Golf Cart Batteries – A Comprehensive Guide
Why test a golf cart after lithium battery installation?
Testing confirms system compatibility, prevents electrical faults, and safeguards your investment. For instance, mismatched voltages between the battery and controller can cause MOSFET failures or erratic acceleration. Always validate connections and BMS alerts before full operation.
Lithium batteries require precise voltage alignment with your cart’s motor and controller. For example, a 51.2V lithium pack (nominal) should peak at 58.4V when fully charged—exceeding this risks controller damage. Use a multimeter to measure voltage at rest and under load (e.g., climbing a hill). Drop below 46V under load? Check for loose terminals or imbalanced cells. Pro Tip: Torque all terminals to manufacturer specs (usually 4–6 Nm) to prevent arcing. Beyond voltage, test thermal performance: lithium cells shouldn’t exceed 50°C during 30-minute drives. Transitioning from lead-acid? Remember: lithium’s lighter weight alters braking distances—test brakes at low speeds first.
What tools are needed for testing?
Essential tools include a digital multimeter, BMS diagnostic app, and infrared thermometer. Advanced setups benefit from load testers or OBD-II scanners for real-time data logging.
A quality multimeter measures voltage (±0.5% accuracy) and continuity, while Bluetooth-enabled BMS apps (e.g., Xiaoxiang) provide cell-level diagnostics. For thermal checks, infrared thermometers detect hotspot variances >2°C between cells. Load testers like the Cadex C7400 simulate 20–50A draws, revealing voltage sag. But what if you lack specialized tools? Use your cart’s hill-climbing ability: a healthy 48V lithium pack should maintain ≥47V on a 15% incline. Pro Tip: Test wiring resistance—any connection exceeding 0.1Ω drops efficiency by 5–10%. For example, corroded terminals add resistance, mimicking a weak battery.
Tool | Basic Use | Advanced Use |
---|---|---|
Multimeter | Voltage checks | Continuity/resistance tests |
BMS App | Voltage monitoring | Cell balancing |
How to check voltage stability?
Measure resting voltage (1 hour post-charge) and under-load voltage. A stable 48V lithium battery should stay within 46–54V during operation, with <3% variance between cells.
Start by testing resting voltage: a 48V pack should read 52–54V after a full charge. Next, drive the cart at maximum load (e.g., uphill with 4 passengers). Voltage dips >10% indicate issues—like a weak cell or undersized BMS. For instance, a pack dropping to 44V under load might have a faulty cell group. Use the BMS app to identify cells deviating >0.2V from others. Pro Tip: Regularly calibrate your multimeter—inaccurate readings can misdiagnose healthy packs. Transitioning from tests? Always recharge to 50–60% if storing the cart long-term. Did you know? Repeated deep discharges (<20%) accelerate lithium battery degradation by 30%.
What safety checks are critical?
Inspect terminal insulation, torque specs, and coolant lines (if liquid-cooled). Exposed terminals or loose bolts risk short circuits, especially in off-road conditions.
Begin with a visual inspection: ensure terminal covers are secure and wiring isn’t frayed. Torque terminals to 4–6 Nm (lithium-specific) using a calibrated wrench—lead-acid specs (8–10 Nm) can strip threads. For liquid-cooled systems, check hose clamps and coolant levels; a leak can drop thermal efficiency by 40%. Pro Tip: Wear insulated gloves when handling high-voltage connections (>60V). After physical checks, validate the BMS’s emergency cutoff: trigger an overload (e.g., stall the motor) to confirm it disengages power within 0.5 seconds. Ever wonder why batteries fail after installation? Often, it’s overlooked insulation faults arcing in humid conditions.
The Importance of Knowing a Golf Cart’s Weight Limit
Fasta Power Expert Insight
Thorough post-installation testing maximizes lithium battery lifespan and safety. At Fasta Power, our batteries feature integrated Bluetooth BMS for real-time diagnostics, ensuring voltage stability within 1% across cells. Always pair our 48V/72V systems with torque-limited terminals (5 Nm) and test thermal performance under regional temperature extremes—lithium thrives in -20°C to 60°C ranges with proper management.
FAQs
Test every 3 months or after 50 cycles. Sudden capacity drops or voltage swings warrant immediate checks.
Can I use a lead-acid battery tester?
No—lead-acid testers apply 15–20A loads, overwhelming lithium BMS. Use lithium-specific testers with 5–10A protocols.
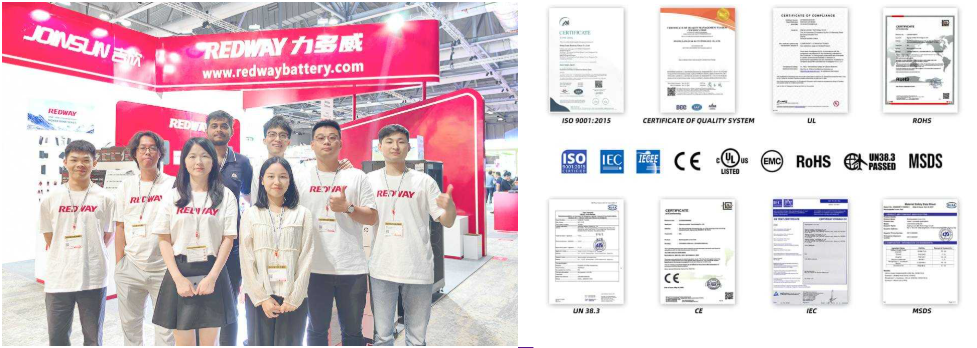