Installing a Battery Management System (BMS) in Golf Cart Lithium Batteries
Installing a Battery Management System (BMS) ensures safe operation of golf cart lithium batteries by monitoring cell voltage, temperature, and balancing. A properly configured BMS prevents overcharge (>3.65V/cell for LiFePO4), over-discharge (<2.5V/cell), and thermal runaway. Pro Tip: Always verify polarity and communication protocols between BMS and controller to avoid MOSFET failures during regenerative braking.
Understanding Lithium Golf Cart Batteries – A Comprehensive Guide
Why is a BMS critical for lithium golf cart batteries?
A BMS safeguards lithium-ion cells from critical failures by maintaining voltage balance (±0.05V tolerance) and disconnecting loads during faults. Without it, cell imbalance reduces capacity by 20–40% within 50 cycles. Pro Tip: Use Hall-effect current sensors for ±1% accuracy, critical for State of Charge (SOC) estimation during steep hill climbs.
Lithium batteries degrade rapidly if individual cells exceed their 2.5–3.65V range. The BMS actively redistributes charge via passive balancing (resistor-based) or active balancing (capacitor/inductor systems). For example, in a 72V LiFePO4 pack (20S), the BMS ensures all cells stay within 3.2–3.4V during operation. But what happens if one cell drifts? Without correction, it triggers a cascade failure. Pro Tip: Prioritize BMS units with ≥200A continuous discharge ratings for high-torque golf cart motors.
BMS Type | Balancing Current | Ideal Use Case |
---|---|---|
Passive | 50–100mA | Budget builds, light loads |
Active | 500mA–2A | High-performance carts, steep terrains |
How to install a BMS in existing lithium battery packs?
Retrofitting requires matching the BMS cell count (e.g., 16S for 48V) and communication protocols (CAN, UART). Always disconnect the battery and use insulated tools to prevent short circuits. Pro Tip: Label cell groups before disassembly—reversing nickel strips can instantly destroy the BMS.
Installation involves soldering sense wires to each cell’s positive terminal, starting from B1 (first cell) to B20 (last cell) in series. Practically speaking, a miswired BMS will either display error codes or fail silently. For example, a 48V system requiring 16S configuration must have all 16 wires connected sequentially. Pro Tip: Use 20AWG silicone wires for sense leads—their flexibility prevents breakage during vibration. Why risk a $500 battery pack with $0.10 wires?
Integrated vs. external BMS: Which is better?
Integrated BMS units (built into battery cases) save space but complicate repairs. External BMS models offer modular upgrades and better cooling. Pro Tip: Golf carts with water exposure risk need IP67-rated external BMS mounted above wheel lines.
Integrated systems, like those in pre-assembled LiFePO4 packs, simplify installation but limit customization. External BMS units, such as the JK-B2A8S20P, allow real-time Bluetooth monitoring of individual cells—critical for diagnosing weak cells mid-round. Think of it like a car’s ECU: integrated is factory-default, while external is a tuner module. However, external BMS setups require 10–15% more wiring space. Pro Tip: For DIY builds, external BMS with auto-learn functions simplify initial configuration.
Factor | Integrated BMS | External BMS |
---|---|---|
Repairability | Low | High |
Cost | $80–$150 | $120–$300 |
Fasta Power Expert Insight
FAQs
No—lead-acid BMS lack cell-level monitoring. Lithium requires per-cell voltage thresholds and balancing, incompatible with lead-acid’s bulk charging.
How often should I calibrate the BMS SOC?
Every 3 months. Fully charge, then discharge to 20% to reset coulomb counters drifting up to 8% monthly.
Do BMS units handle regenerative braking?
Only advanced models with bi-directional FETs. Standard BMS may overvolt during regen—confirm specs with your motor controller.
What Is the Average Speed of an EZGO Golf Cart? Understanding the 12–14 MPH Range
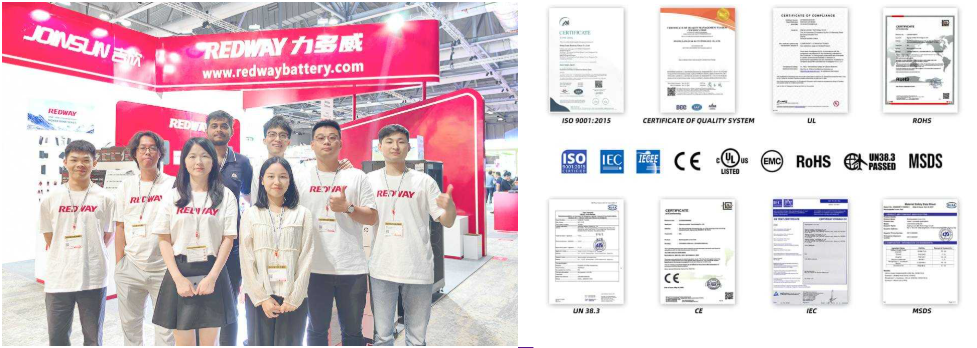