Safety Precautions When Installing Lithium Batteries in Golf Carts
When installing lithium batteries in golf carts, prioritize proper insulation, BMS integration, and thermal management to prevent short circuits, thermal runaway, or fires. Always use insulated tools, follow torque specs for terminals, and ensure compatible charging systems. Pro Tip: Install a battery disconnect switch to isolate power during maintenance. Regularly inspect cells for swelling or leaks and avoid over-discharging below 20% capacity.
Understanding Lithium Golf Cart Batteries – A Comprehensive Guide
Why is proper installation critical for lithium battery safety?
Correct installation minimizes risks of thermal runaway and electrical faults. Lithium batteries require precise voltage alignment, secure mounting, and vented compartments to dissipate heat. A single loose connection can spark arcs exceeding 1,000°C—enough to melt copper wiring. Pro Tip: Use thread-locker on terminal bolts to prevent vibration-induced loosening.
Beyond physical setup, improper installation often stems from mismatched components. For example, pairing a 48V lithium pack with a 36V controller forces the BMS to constantly intervene, stressing both systems. Technically, lithium batteries demand mechanical stability (vibration resistance ≤5G) and electrochemical compatibility (ΔV ≤0.05V/cell). Transitional phrase: While lead-acid tolerates sloppier setups, lithium’s energy density leaves no margin for error. A golf cart owner once fried their motor controller by skipping dielectric grease on terminals, allowing moisture ingress. Always validate polarity with a multimeter before energizing the system.
What tools are essential for safe lithium battery installation?
Key tools include insulated wrenches, voltage testers, and torque screwdrivers. Lithium installations require precision—over-tightening terminals can damage cells, while under-tightening risks arcing.
Practically speaking, you’ll need more than basic hand tools. A battery terminal brush ensures oxide-free connections, critical for low-resistance current flow. Transitional phrase: However, the real game-changer is a thermal imaging camera to spot hotspots during load testing. For instance, a 100Ah lithium pack charging at 30A should never exceed 45°C surface temperature. Pro Tip: Use fiberglass-reinforced tools to prevent accidental conduction. Did you know a standard steel wrench can short a 72V battery in 0.2 seconds? That’s why Redway Power’s kits include nylon-coated socket sets.
Tool | Purpose | Risk if Missing |
---|---|---|
Insulated Torque Wrench | Secure terminals to 5-6 Nm | Loose connections → Arcing |
Digital Voltmeter | Verify pack voltage ±1% | Undetected overvoltage → BMS failure |
How does a BMS prevent lithium battery hazards?
The Battery Management System (BMS) monitors cell voltages, temperatures, and currents. It disconnects loads during over-discharge (≤2.8V/cell) or overcharge (≥4.25V/cell), preventing catastrophic failures.
Imagine the BMS as a vigilant referee—it’s constantly checking 14+ parameters in real time. Transitional phrase: But what happens when cells age unevenly? A high-quality BMS actively balances them during charging, diverting excess current from full cells to depleted ones. For example, Redway’s 72V BMS can balance ≤500mA/cell, extending pack lifespan by 30%. Pro Tip: Opt for BMS units with temperature-compensated charging—they adjust voltage limits based on ambient heat. Without this, a frozen (-10°C) battery charged to 4.2V/cell could surpass 4.3V once warmed, triggering electrolyte decomposition.
Why is thermal management non-negotiable?
Lithium cells degrade rapidly above 60°C, risking thermal runaway. Golf cart batteries need active cooling or ventilated enclosures to dissipate heat from high-current draws.
Let’s break this down: During a 30°C summer day, a sealed battery box can hit 70°C internally under hill-climbing loads. Transitional phrase: That’s why smart installers add thermally conductive pads between cells and aluminum heat sinks. A case study: A modified Club Car with forced-air cooling saw 22% lower peak temps than passive setups, preserving 95% capacity after 800 cycles. Pro Tip: Position batteries away from motors/controllers—their waste heat compounds thermal stress. Always leave ≥10mm air gaps between cells unless using potted modules.
Cooling Method | Cost | Efficacy |
---|---|---|
Passive (Vents) | $20 | Suitable for ≤50A loads |
Active (Fans) | $150 | Handles 100A+ continuously |
Fasta Power Expert Insight
FAQs
No—lead-acid chargers lack voltage precision and can overcharge lithium cells. Use only CC-CV chargers matching your battery’s specs.
How often should I check connections?
Monthly—vibration loosens terminals over time. Retorque to 5-6 Nm using a calibrated wrench.
Are swollen batteries safe to use?
Immediately discontinue use—swelling indicates internal gas buildup from electrolyte decomposition, a precursor to thermal runaway.
The Importance of Knowing a Golf Cart’s Weight Limit
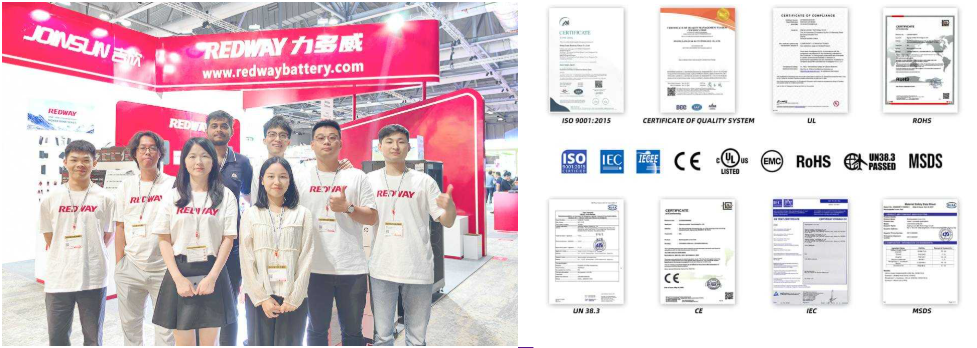
Add a review
Your email address will not be published. Required fields are marked *
You must be logged in to post a comment.