What Are the Best Heavy-Duty Truck Batteries for Longevity?
Heavy-duty truck batteries are specialized power sources designed for commercial vehicles, offering high cranking power, deep-cycle resilience, and extended lifespan. Key features include robust construction, vibration resistance, and compatibility with extreme temperatures. Top options include AGM (Absorbent Glass Mat), lithium-ion, and flooded lead-acid batteries, with AGM being preferred for maintenance-free operation and superior durability in demanding conditions.
What Batteries Do Cell Phone Towers Use? A Comprehensive Guide
How Do Heavy-Duty Truck Batteries Differ From Regular Car Batteries?
Heavy-duty truck batteries use thicker lead plates, enhanced electrolyte formulations, and reinforced casings to withstand vibrations and heavy electrical loads. They provide higher cold cranking amps (CCA) and reserve capacity (RC) than standard car batteries, ensuring reliable starts and sustained power for auxiliary systems like refrigeration units or hydraulic lifts.
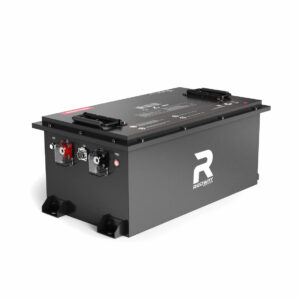
What Are the Key Features of a Reliable Heavy-Duty Truck Battery?
Critical features include high CCA (800+), RC above 180 minutes, spill-proof design, corrosion-resistant terminals, and vibration-dampening mounts. Advanced options offer smart technology for charge monitoring, thermal stability for -40°F to 140°F operation, and compatibility with regenerative braking systems in modern trucks.
Which Battery Technologies Dominate the Heavy-Duty Truck Industry?
AGM batteries lead due to leak-proof safety and deep-cycle endurance. Lithium-ion is gaining traction for weight savings (up to 60% lighter) and faster charging. Flooded lead-acid remains cost-effective for short-haul fleets, while gel batteries serve niche applications requiring extreme temperature tolerance.
How Can You Extend the Lifespan of a Heavy-Duty Truck Battery?
Maintain clean terminals with anti-corrosion spray, ensure proper voltage (13.6-14.4V charging), avoid deep discharges below 50%, and use temperature-compensated charging. Monthly equalization charges for flooded batteries and load testing every 6 months can add 2-3 years to battery life.
What Are the Warning Signs of a Failing Truck Battery?
Symptoms include slower engine cranking, dimming headlights during startup, swollen battery case, sulfur smells, and frequent jump-starts. Voltage drops below 12.4V at rest or failure to hold 9.6V during cranking (SAE J537 test) indicate imminent failure.
How Does Temperature Affect Heavy-Duty Battery Performance?
Cold reduces CCA by 35% at 0°F, while heat above 100°F accelerates electrolyte evaporation. Optimal performance occurs between 50°F-85°F. Thermal management systems in premium batteries use phase-change materials or active cooling to mitigate these effects, maintaining 95% efficiency across extremes.
Battery chemistry plays a crucial role in temperature resilience. AGM batteries retain 85% of their rated CCA at 0°F due to absorbed electrolytes preventing freezing, whereas flooded batteries may lose up to 50%. Lithium-ion variants excel in cold starts, delivering 90% of their capacity at -20°F but require heated enclosures below -40°F. In desert conditions, gel batteries outperform others with 30% less water loss compared to flooded designs. Fleet managers in extreme climates often install insulated battery boxes with thermostatically controlled fans, reducing temperature-related capacity loss by up to 40%.
Battery Type | Cold Weather Performance | Heat Tolerance |
---|---|---|
AGM | 85% CCA at 0°F | 125°F max |
Lithium-ion | 90% CCA at -20°F | 140°F max |
Flooded | 50% CCA at 0°F | 115°F max |
What Maintenance Practices Optimize Truck Battery Efficiency?
Implement bi-weekly terminal cleaning, monthly state-of-charge checks with refractometers (flooded) or conductance testers (AGM), and annual capacity testing. For fleets, centralized battery management systems track cycle counts, recharge efficiency, and sulfation trends across all units.
Advanced maintenance protocols incorporate ultrasonic cleaning for terminal corrosion and infrared thermography to detect hot spots. AGM batteries benefit from quarterly equalization charges at 15.5V for 4 hours to prevent stratification. For lithium-ion systems, calibrating the battery management system (BMS) every 500 cycles ensures accurate state-of-charge readings. Fleet operators using telematics report 18% longer battery life through predictive maintenance alerts for voltage deviations exceeding ±0.2V from baseline. Always store spare batteries at 50% charge in climate-controlled environments to minimize calendar aging.
“The shift toward lithium-ion in heavy trucks isn’t just about weight—it’s about total cost of ownership. Our fleet data shows 23% lower maintenance costs and 40% faster turnaround times at charging stations. However, proper battery management system integration with the truck’s ECU is critical to prevent thermal runaway risks.”
– Fleet Technology Director, Major Logistics Firm
FAQs
- Q: Can I use automotive batteries in heavy trucks temporarily?
- A: Not recommended—commercial batteries have 2-3x thicker plates to handle vibration. Automotive units risk premature failure under truck loads.
- Q: How often should heavy-duty batteries be replaced?
- A: Typical replacement cycles: flooded (3-5 years), AGM (4-7 years), lithium-ion (8-12 years), depending on discharge depth and maintenance.
- Q: Are lithium truck batteries DOT-approved?
- A: Yes, but must meet FMVSS 538 and UL 2580 standards. Always verify UN38.3 certification for transport safety.