What Are the Challenges Faced by Golf Cart Lithium Battery Manufacturers Today?
Golf cart lithium battery manufacturers face multifaceted challenges including technological innovation pressures, global supply chain complexities, and stringent environmental regulations. High R&D costs for energy density improvements and thermal management systems compete with evolving market demands for affordability. International trade policies and regional certification requirements (e.g., UL 2580, UN38.3) further strain production scalability. Labor shortages in Western markets exacerbate operational costs, while rising material prices for cobalt and nickel destabilize profit margins.
Understanding Lithium Golf Cart Batteries – A Comprehensive Guide
How does technological advancement impact competitiveness?
Energy density optimization and cycle life enhancements dominate R&D priorities. Manufacturers must develop cobalt-free cathodes and advanced BMS to meet 2,000+ cycle expectations while reducing costs by 15–20% annually to stay competitive against lead-acid alternatives.
Transitioning to silicon-anode or solid-state technologies requires capital investments exceeding $200M per production line. For example, Tesla’s 4680 cell production faced 18-month delays due to dry-coating tech hurdles. Pro Tip: Tier 1 suppliers prioritize partnerships with material science firms to secure IP for next-gen electrolytes. A 10% increase in energy density can extend golf cart range by 25 km per charge—critical for resorts and golf courses. However, does faster innovation risk premature obsolescence of existing inventory? Companies like CATL allocate 8–12% of annual revenue to R&D to maintain leadership.
What supply chain risks affect lithium battery production?
Geopolitical volatility in lithium-producing nations (Chile, Australia) and graphite export restrictions (China controls 70% of anode material supply) create pricing unpredictability. Cobalt spot prices fluctuated 38% YoY in Q2 2025.
Manufacturers require dual sourcing strategies—57% of U.S. firms now use Mexican or Canadian suppliers for critical materials to comply with IRA localization rules. The table below compares regional supply risks:
Material | Primary Source | Inventory Buffer (Days) |
---|---|---|
Lithium Carbonate | Australia (52%) | 45–60 |
Nickel Sulfate | Indonesia (28%) | 30–45 |
When Indonesia banned nickel ore exports in 2023, battery-grade sulfate prices spiked 62% in three months. Pro Tip: Vertical integration through mining stakes—BYD’s $1B Bolivian lithium investment secured 15-year supply at fixed rates. But how scalable are these models for mid-sized manufacturers? Logistics bottlenecks at major ports (e.g., Long Beach congestion caused 33-day delays in 2024) necessitate regionalized warehousing networks.
How do environmental regulations constrain manufacturing?
EPA’s Hazardous Waste Generator rules and EU Battery Directive 2027 mandate 95% recyclability and carbon footprint labeling. Non-compliance fines reach 4% of global revenue.
Water treatment systems for electrode slurry production cost $8–12M per facility—33% of golf cart battery makers lack compliant wastewater infrastructure. California’s Prop 65 requires toxicological assessments for all battery components, adding $500K–$1M per product line. For example, a Nevada-based plant faced $2.3M penalties for improper solvent storage. Practically speaking, manufacturers must adopt closed-loop recycling like Redwood Materials’ 96% recovery process. Transitional strategies include:
Strategy | Cost Impact | Timeline |
---|---|---|
ISO 14001 Certification | +18% OPEX | 12–18 Months |
Onsite Recycling | +$9M Capital | 24–36 Months |
Why is workforce development a critical challenge?
Automation engineers and electrochemical specialists face global shortages—32% of battery plants operate below 75% staffing capacity. U.S. labor costs rose 50% since 2020, exceeding inflation by 19 points.
Northvolt’s Swedish gigafactory delayed production by two years due to insufficient skilled technicians for dry room operations. Training programs require 6–9 months per worker—Proterra’s South Carolina plant invests $25K annually per employee. But can smaller manufacturers sustain this? Collaborative models like Michigan’s Battery Workforce Initiative partner colleges with manufacturers to certify 1,200 workers yearly. Real-world example: A Florida assembly line lost $7.4M in potential revenue from 12 vacant BMS engineer positions over eight months.
Fasta Power Expert Insight
FAQs
USMCA rules of origin require 75% North American content for tariff exemptions—importing Asian cells adds 6–8% duty costs unless localized with domestic assembly.
Can lithium batteries meet golf cart weight limits?
Yes—LiFePO4 packs weigh 60% less than lead-acid equivalents. Always verify chassis load capacity; our 72V 100Ah model reduces total weight by 118kg versus SLA configurations.
The Importance of Knowing a Golf Cart’s Weight Limit
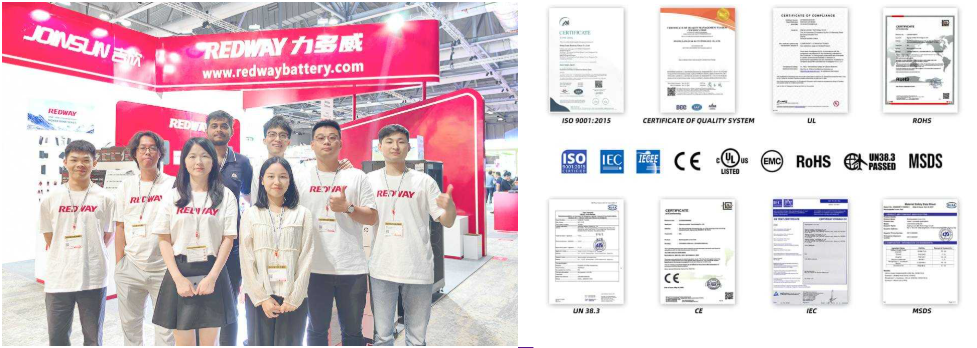
Add a review
Your email address will not be published. Required fields are marked *
You must be logged in to post a comment.