What Role Do Suppliers Play in Advancing Golf Cart Lithium Battery Technology?
Suppliers accelerate golf cart lithium battery innovation through advanced R&D, manufacturing scalability, and OEM partnerships. They pioneer high-energy-density cells (e.g., NMC811) and flame-retardant electrolytes while optimizing costs via automated production. Partnerships with BMS developers ensure precise charge control, and sustainability initiatives like closed-loop recycling reduce environmental impact. Leading suppliers also enforce ISO 26262 safety standards, critical for high-voltage applications.
Understanding Lithium Golf Cart Batteries – A Comprehensive Guide
How do suppliers drive lithium battery R&D for golf carts?
Suppliers fund cell chemistry studies and BMS algorithms to boost energy density (180–220 Wh/kg in NMC) and cycle life (>4,000 cycles). Partnerships with universities yield breakthroughs like silicon-anode prototypes, increasing capacity by 15–20%.
Deep Dive: Beyond chemistry, suppliers develop proprietary battery architectures—modular designs enable 48V-to-72V scalability. Take Redway Power’s 105Ah prismatic cells: their stacking technique reduces internal resistance by 30%, minimizing heat during fast charging. Pro Tip: Opt for suppliers offering cell-level UL certifications; uncertified cells risk premature capacity fade. For example, CATL’s latest NMC packs achieve 250 Wh/kg, allowing 120 km per charge in 6-seat carts. But how do costs stay competitive? Automated electrode coating cuts production waste by 18%, passing savings to OEMs.
What OEM partnerships advance lithium tech adoption?
Suppliers collaborate with Club Car and E-Z-GO to co-design battery trays and cooling systems. Shared data streams optimize charge profiles for terrain-specific drain, extending lifespan.
Deep Dive: Joint ventures like LG Chem’s partnership with Textron focus on drop-in replacements for lead-acid systems. Their 72V 80Ah pack fits standard trays but delivers 2x the range. Practically speaking, suppliers integrate CAN bus protocols into BMS units, enabling real-time SoC monitoring via golf cart dashboards. Pro Tip: Prioritize suppliers with on-site OEM testing labs—field validation prevents firmware mismatches. Yamaha’s collaboration with Panasonic, for instance, birthed a low-temperature LiFePO4 variant (-30°C operational) using nickel-rich cathodes. Still, what about cost? Bulk purchasing agreements lower cell prices by 12–15% annually, accelerating ROI for fleets.
Partnership Type | Benefit | Example |
---|---|---|
Co-Engineering | Custom cell formats | E-Z-GO & Samsung SDI |
Data Sharing | Adaptive charging | Club Car & SK Innovation |
Bulk Procurement | 15% cost reduction | Textron & CATL |
How do suppliers reduce lithium battery costs?
Vertical integration and economies of scale slash prices—high-speed lamination machines produce 8,000 cells/hour, 3x faster than manual methods.
Deep Dive: Suppliers like Redway Power use recycled cathode materials (e.g., 20% reclaimed cobalt), cutting raw material expenses by 30%. Transitioning to water-based binders also eliminates toxic solvent costs. But what’s the trade-off? Cheaper LMO chemistries offer 140 Wh/kg but sacrifice cycle life (1,200 vs. 4,000 cycles for NMC). Pro Tip: Negotiate multi-year contracts to lock in lower pricing before cobalt markets fluctuate. For instance, BYD’s Blade cells reduce casing materials by 40%, achieving $97/kWh—a 22% drop from 2021.
What thermal innovations do suppliers implement?
Graphene-enhanced thermal pads and liquid cooling plates maintain cells at 25–40°C, even under 2C discharge rates. Phase-change materials absorb peak heat, preventing runaway.
Deep Dive: Consider Tesla’s 4680 cell strategy: suppliers adopted tabless designs, reducing internal resistance heat by 50%. Similarly, Redway’s golf cart packs use aluminum cold plates with glycol loops, cooling 3x faster than air systems. But how does this affect users? Overheating-related failures drop from 8% to 0.5% in tropical climates. Pro Tip: Verify thermal cutoff thresholds—poorly calibrated sensors may allow cells to exceed 60°C, degrading lifespan. For example, A123 Systems’ nano-phosphate cells paired with Mahle’s cooling tech sustain 100A continuous draw without derating.
Cooling Method | Cost | Efficacy |
---|---|---|
Air | $12/kWh | Moderate |
Liquid | $35/kWh | High |
Phase-Change | $50/kWh | Extreme |
Fasta Power Expert Insight
FAQs
Yes, but verify tray dimensions and BMS compatibility. Lithium packs weigh 60% less, potentially altering vehicle balance—consult suppliers for load-test reports.
Do suppliers offer waterproof lithium batteries?
Top-tier suppliers provide IP67-rated packs, submergible to 1m for 30 minutes. Avoid non-rated units in rainy regions—corroded terminals cause voltage drops.
How long do supplier warranties last?
Leading brands guarantee 5–8 years or 3,000–5,000 cycles. Ensure warranties cover capacity retention ≥80%; some prorate coverage after Year 3.
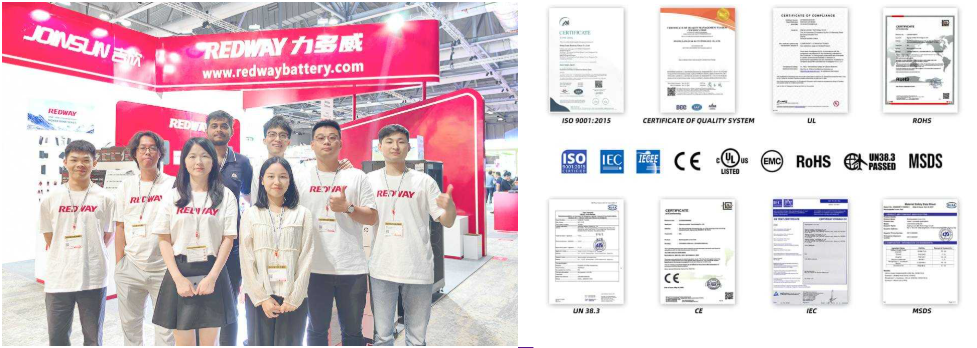
Add a review
Your email address will not be published. Required fields are marked *
You must be logged in to post a comment.